Intro to the metal lathe
Metal lathes are versatile tools that we use to make precise round parts. These kinds of precise round parts show up in everything from small consumer goods to heavy industrial machinery, and they make smooth and efficient movement possible. Metal lathes achieve this through accurate linear movement and rigidity, which allows us to make parts with exacting dimensions and concentric features. In this class, we'll learn how to safely operate the manual metal lathes, produce some simple parts, and explore some of the many ways we can fabricate parts with a manual metal lathe.
How Does a Metal Lathe Work?
Overview
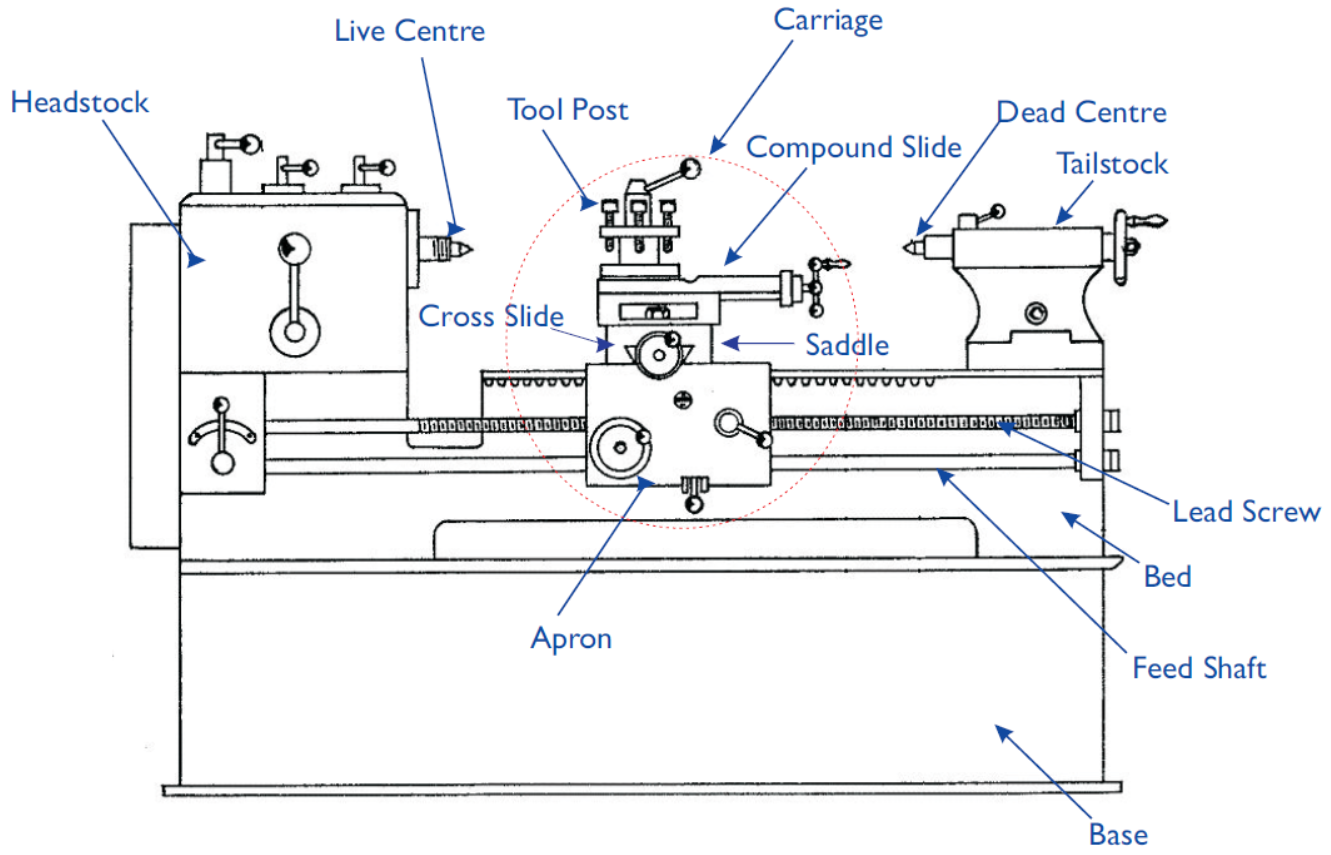
The lathe holds material securely and spins it along the axis of the spindle bore. As the material spins, operators can move a cutting tool against the work parallel to the spindle bore with the carriage, which travels along the ways, the prismatic rails on the bed of the ways. Users can also move the tool perpendicular to the work with the cross slide, and at a compound angle with the compound (often referred to as the top slide). Users can adjust the depth of cut by adjusting these controls in unison, allowing them to make round, concentric features with precise dimensions.
Concentricity: the Superpower of a Metal Lathe
The spindle of the lathe spins in an accurate circle, so every cut will produce a feature concentric with the spindle axis. The lathe has precisely machined axes, so the carriage will move parallel to the spindle axis, and the cross slide will move perpendicular to the spindle axis. Turning cuts with the carriage will produce precise cylindrical features, while facing cuts with the cross slide will produce flat surfaces perpendicular to the spindle axis.
Rigidity: the Corollary to the Metal Lathe Superpower
The ways of the lathe are parallel to the spindle bore, and the cross slide movement is perpendicular to the spindle bore. Ideally, all cuts would follow these parallel and perpendicular constraints, but the intense cutting forces cause all of the components -- the work, the tools, and even the lathe itself -- to flex to some degree. We try to minimize this by building the lathe out of sturdy materials; the South Bend 9A, the smallest lathe in the machine shop, weighs over a half a ton. We also reduce the amount of flex by limiting both tool and material stick-out and controlling the aggressiveness of our cuts.
Metal Lathe Safety
The biggest safety hazard with the metal lathe is getting snagged by the spinning chuck or the work it's holding. Do not wear rings, watches, jewelry, gloves, or loose clothing that could be caught in the chuck. Tie back long hair before using the lathe, and keep your hands clear of the headstock while the lathe is spinning.
One lathe specific hazard is the hazard of an unattended chuck key flying out of the chuck when the lathe turns on. Pay attention to where you pick up the chuck key and where you put it down after adjusting the chuck; unless you're actively adjusting the chuck, the key should be outside of the chuck and away from the headstock.
General shop safety rules apply too. You must wear safety glasses and closed toed shoes in the machine shop, regardless of whether you're using any machinery. Review the safety guidelines on the metal lathe overview page for more guidance.
Operating the Lathe
South Bend 9A
Installing and removing the chuck
The South Bend 9A has a threaded spindle. Remove the chuck by locking the spindle into back gear and using a chuck key and mallet to loosen the chuck from the spindle
[picture of back gear] [picture of chuck, key, mallet]
Install a new chuck by reversing this process; screw the back of the chuck onto the threads of the spindle. The rotation of the spindle will tighten the threads of the chuck to the threads of the spindle, so you don't need the mallet to lock the chuck to the spindle.
Changing the Spindle Speed
Belts and Pulleys
The South Bend has two belts. The V-belt between the motor and the lathe drive shifts between high range and low range, and the flat belt between the lathe drive and the spindle allows adjustments within these ranges. To adjust the speed, loosen the belt tension lever on the left side of the machine, then move the belts to achieve the appropriate speed. Tighten the belt tension when you're ready to use the lathe
[picture of belt tension lever] [picture of motor/lathe drive pulleys] [chart of lathe speeds]
Back Gear
The back gear control on the lathe allows low speed, high torque rotation. To use the back gear, pull the back gear lever until the back gears engage with the spindle gear. If the gears are not meshing, manually spin the chuck while pulling the back gear lever to the rear.
Next, pull the coupling pin out of the largest drive gear. If you don't remove this pin, the chuck and gears will be locked. This will prevent the spindle from turning, and it's useful for loosening the chucks, but operating the lathe in this condition will cause the belts to rub.
The additional mechanical components in the back gear drivetrain creates more mechanical, gear-clanging noise. This noise is normal, but grinding or rubbing noises are not. Stop the lathe if you hear these kinds of noises.
To disable the back gear, move the back gear lever to the rear to disengage the back gear and re-insert the coupling pin. Ensure that the pin is fully seated in the cutout, which is in-line with the oil port on the middle spindle pulley.
[picture of back gear mechanism and oil port]
Power Feed
The South Bend has both power carriage feed and power cross feed. The keyway in the leadscrew powers this power feeding, so the leadscrew must be enabled to use power feed. With the lathe powered off, enable the power feed by moving the power feed lever out of the neutral position and into the appropriate direction. Note that turning and facing operations typically require different power feed lever settings.
[ picture of power feed lever on headstock] [picture of power feed lever and clutch on the apron]
With the lathe still powered off, move the power feed lever on the apron to the appropriate setting. Loosen the clutch knob to disengage the power feed before turning on the lathe. Tighten the clutch knob to engage the power feed, and confirm that the correct control knob is turning in the correct direction. Disengage the power feed by loosening the clutch.
Two levers control the speed of the power feed. The leftmost position of these levers is the fastest feed speed, while the rightmost position is the slowest. Position E has a good range of feed rates, and this is typically the right setting for the first lever.
[pic of power feed levers] [feed rate chart]